Founded in 1989, Haomei Machinery has been at its best age for we have rich experience to design and manufacture the right concrete batch plant for you. Perfect supporting equipment including concrete mixer truck, concrete pumping truck, concrete pump trailer, realizes the delivery and use of quality concrete from the batching site to the construction site.
2024年6月25日星期二
Working Flow of Stationary Concrete Batching Plant in Maldives
2024年6月12日星期三
Why Should You Choose A Self-Loading Concrete Mixer Truck
The self-loading concrete mixer truck is equipment used to mix and transport concrete on site. Owning a self-loading mixer truck is equivalent to owning a loader, concrete mixer, concrete mixer truck and more than 6 workers.
The self loading concrete mixer truck meets the need of most engineering construction projects at home and abroad, because most of the concrete are designed with large slump, large fluidity and easy molding. The 3.5m3 self-loading concrete mixer truck is more popular in the market.
The self loading transit mixers are new concrete mixers suitable for projects such as general highways, power stations, construction sites, dam construction, hydropower, roads, bridges, and large and medium-sized prefabrication plants. It has the advantages of low energy consumption, stable operation, compact structure, light weight, and higher production efficiency.
Especially in some small projects, the use of self-loading mixer trucks has become more and more common. The reason for this is that in the past, the construction site needed to go to the concrete batching plant to buy concrete, but the time cost and vehicle cost were too high during the transportation process. Therefore, many construction parties now use the method of producing concrete on site to save costs.
The mobile self loading concrete mixer truck adopts metering technology with independent intellectual property rights, which can accurately calculate the proportion of concrete materials and ensure the homogeneity and quality stability of concrete. There are also professional mixing systems and guide plates during the mixing process to ensure that the mixing effect reaches the best state, greatly improving production efficiency.
There is a large loading shovel next to the cab of the self propelled concrete mixer truck The driver operates in the cab, and the loading arm can perform a series of lowering, shoveling, and raising actions. After a worker arranges the materials, the driver operates the loading arm to drop and shovel the materials. After the shoveling is completed, the driver operates the loading arm to rise to the mouth of the mixing tank. The driver continues to operate to open the rear opening of the bucket, and the material in the bucket can enter the mixing tank accurately.
Original Source: https://www.self-loading-mixer.com/a/why-should-you-choose-a-self-loading-concrete-mixer-truck.html
What Are Features of Drum Mix Asphalt Plant
Asphalt mixing equipment puts various aggregates and asphalt into the equipment at one time according to the standard proportion and standard industrial process, and forcefully mixes these aggregates and asphalt. As long as the degree of fusion of aggregates and asphalt reaches a certain precision, the finished material is formed. If the proportion of a certain aggregate is not enough, the amount of aggregate can be increased intermittently to achieve the standard precision.
The characteristics of the continuous asphalt drum mix plant process are: dynamically metered and graded cold aggregate and stone powder continuously enter from the front of the mixing drum, then dried and heated by downstream heating, mixed with dynamically metered and continuously sprayed hot asphalt at the rear of the drum, and asphalt concrete is continuously stirred by drop mixing.
Compared with batch type hot mix plant, continuous hot mix asphalt trailer has cold aggregate drying and heating and mixing in one, so the process is simplified and the manufacturing and use costs are low. Dust is difficult to escape when mixing concrete, and it is easy to meet environmental protection standards.
However, since the heating of aggregates is carried out by hot air in the direction of material flow, the utilization rate of heat energy is low, and the water content of the mixed asphalt concrete is large and the temperature is also low. Simple and economical drying drums guarantee high production capacity and high quality of the finished product, with precise inspection of the raw materials.
As in conventional plants, the asphalt produced in the dry mixer drum is sent to storage silos and then unloaded into transport trucks for transport to the road construction site. It can be easily set up near road construction areas, allowing for rapid asphalt production and seamless integration into the construction process.
Continuous asphalt mixing equipment is currently widely used around the world, especially in North America, South America, France and other regions, accounting for a considerable market share. The production capacity of the whole equipment ranges from 20-60 tons/hour.
There are two different types of continuous drum mix plants: Co-current heated drum mixers (the simplest and cheapest type of plant) and counter-current heated plants (more efficient from a heat exchange perspective). Welcome to inquire drum mix plant price from us directly.
Original source: https://www.haomei-machinery.com/a/what-are-features-of-drum-mix-asphalt-plant.html
How to Maintain Ready Mix Concrete Pump
The ready mix concrete and pump is a heavy mechanical equipment, mainly used to transport concrete from the concrete mixer truck to high-rise buildings, bridges and tunnels. Concrete pump trailer has many advantages: It has high efficiency. The hydraulic system of the pump trailer can transport concrete to higher buildings or tunnels at high pressure, thereby improving work efficiency and reducing construction time.
The hydraulic system is the most critical part of the concrete pump, and it is inextricably linked to the pumping effect of the equipment. Although the concrete pumps produced by Haomei Machinery adopt quality main oil pumps imported from Germany's Hawe, Rexroth, and Japan's Kawasaki, is still needs to be maintained frequently.
The steps for maintaining the concrete pump are to check whether the hydraulic pipeline is leaking. If there is oil leakage, it needs to be tightened. If it continues to leak after tightening, the corresponding parts need to be replaced. Check whether the bolts and nuts of the hydraulic system, especially the high-pressure pipeline, are loose. If they are loose, they should be tightened immediately.
Check the hydraulic oil. The suitable ambient temperature for the hydraulic system should be within 30 degrees Celsius and well ventilated. If the oil temperature is still over 70 degrees Celsius after the radiator is turned on, the hydraulic system will fail. The hydraulic system should be repaired before continuing to work.
When refueling for the first time, the oil level in the hydraulic oil tank should be checked, and the oil should be added when the oil level is low. The color of the hydraulic oil can be observed to determine whether the hydraulic oil has deteriorated. If it is non-transparent or discolored, the hydraulic oil should be replaced in time.
In addition to checking the hydraulic pipelines and hydraulic oil, the following aspects of the hydraulic concrete pump also need to be checked: the movement of each hydraulic control part should be flexible and the connection should be reliable. The valve group of the concrete pump hydraulic system works sensitively and has no neutral position. The system working pressure meets the requirements of the manual.
The cooling pump works effectively, the oil temperature does not exceed 80℃, the pipeline connection should be reliable, without rust, deformation, aging, damage, and oil leakage. The hydraulic oil type, oil quality, oil quantity and use comply with relevant regulations. The working capacity of the main oil pump should reach the rated value.
Original source: https://www.concrete-pump-cn.com/a/how-to-maintain-ready-mix-concrete-pump.html
Which One to Choose: Vertical or Horizontal Cement Silo
Among the components of a concrete batching plant, the cement storage is very important. So, should we choose a horizontal cement silo or a a vertical cement silo when building a concrete mixing station? What are the specific differences and how to choose?
The difference between cement horizontal silos and vertical cement silos mainly lies in the foundation, the height of the equipment, the applicable place, the role of weighing cement, the shape and appearance, etc.
DIFFERENT FOUNDATION
Horizontal cement silos do not require foundations and can be installed as long as the land is leveled. Horizontal cement silos are welded from container plates, with high strength, good sealing, easy disassembly and assembly, short installation cycle, and easy to move frequently.
Due to the height limitation of the silo, the vertical cement silo needs a foundation before installation, and can only be installed after the foundation is firm. After the construction site is completed, it needs to be processed on site and cannot be transferred completely.
DIFFERENT HEIGHTS
The bottom of the horizontal cement silo is supported by several legs, which is very convenient for disassembly and assembly. The transportation height and width are within the limit. It can be transported on the road using an ordinary truck, and can be transferred and recycled after the project is completed.
The height of the vertical cement silo is relatively high, usually about 8-15 meters in use. During transportation, it is limited in height, width and length, and it is inconvenient to enter and exit the construction site.
DIFFERENT APPLICATION SCOPE
After the vertical cement silo is installed, the overall height is relatively high, and it is necessary to do a good job of wind and lightning protection. It cannot be used in places with limited height, such as corridor grouting construction. It is usually used for the storage of cement, sand, fly ash and other powder materials in concrete mixing plants and large mortar plants.
After installation, the overall height of the mobile cement silo is low, and the overall length is suitable for the storage of various bulk materials such as cement, fly ash, bentonite, etc. in the corridor.
WITH WEIGHING SYSTEM OR NOT
After the vertical cement silo is filled with cement, the center of gravity is high, and the weighing system cannot be installed, and the weight of the cement in the silo cannot be accurately reflected.
The weighing sensor is installed at the bottom of the horizontal cement silo to reflect the weight of the cement in the silo in real time. It can be used with the intelligent pulping system to realize automatic output after cement weighing.
DIFFERENT SHAPES
The vertical cement silo is a vertical, cylindrical equipment with high outrigger height. Horizontal cement silo is a horizontal, square equipment with low outrigger height.
Generally speaking, a small cement tank, such as a 30T cement tank, has a diameter of about 2.5 meters and a height of 5 meters. A cement tank of about 50T can be made into a diameter of 2.6 meters or a diameter of 3 meters, and the corresponding height is 8 or 6 meters. A cement silo 100 ton is a more commonly used model, with a diameter of 3 meters and a height of 11 meters. Welcome to leave message below o inquire cement silo 100 ton price.
Original source: https://www.concretebatchplanthm.com/a/which-one-to-choose-vertical-or-horizontal-cement-silo.html
What Will Sicoma Twin Shaft Mixer Bring to HZS25 Concrete Batching Plant
In the construction industry, the choice of concrete mixing plant directly affects the efficiency and cost of the project. In recent years...
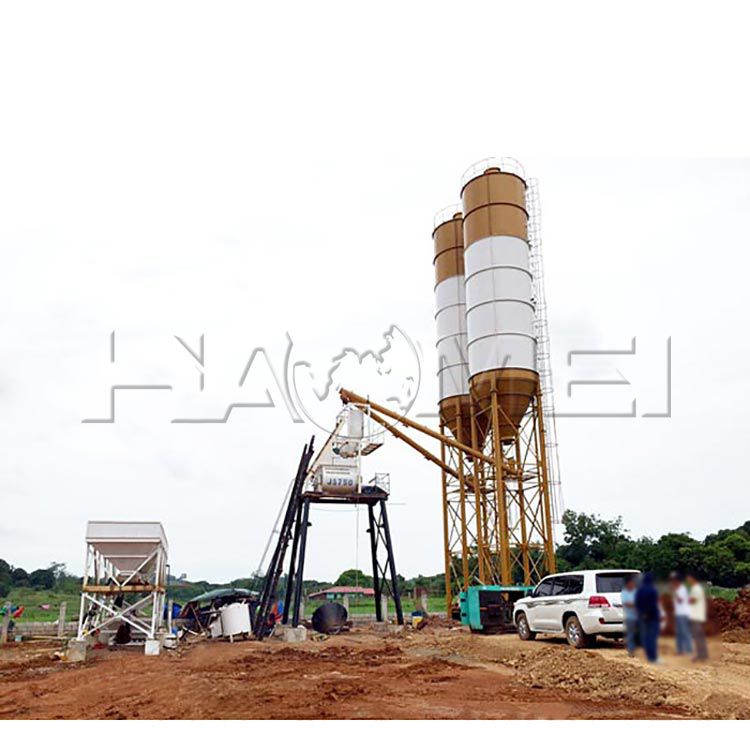
-
The ready mix concrete plant is a complete set of equipment for producing high-quality concrete. It is widely used in various types of bui...
-
Among the components of a concrete batching plant, the cement storage is very important. So, should we choose a horizontal cement silo or ...
-
Haomei has 1060/1100/8011/8021/8079 aluminum foil for pharmaceutical packaging. If you need, don't hesitate to contact us:dolly@al...